
MTS Tumbler screening machines
Modular design for easy handling
- Model sizes: 600 – 1000 – 1200 – 1600 –2000 – 2400 and 2600 mm in diameter, with up to 5 decks
- Specifications: mild steel, stainless steel or finishing on choice
- Circular construction with central material feed, variable outlet positions and easy to clean
- Automatic centring of the screens
- Food-safe U-shaped silicon gaskets enable easy fitting
- Patented adjustment system allows the operating parameters to be set quickly and simply
- Screening motion independent of throughput
- No oversize grains in the fine material
- Fragile materials and agglomerates are not destroyed
- Particularly suitable for very lightdense materials
- Machines are shipped ready for operation and preset for the relevant product – in 90 per cent of all cases no further adjustment is necessary
- Low height and modest power requirements
- Compatible with other tumbler screen machines
- MINOX-patented Pneumatic lifting system for fast and save screen exchange
- MINOX-patented baloncing system for low dynamic loads on foundation
Model | MTS 600 |
MTS 1000 |
MTS 1200 |
MTS 1600 |
MTS 2000 |
MTS 2400 |
MTS 2600 |
---|---|---|---|---|---|---|---|
Diameter (mm) | 600 | 1000 | 1200 | 1600 | 2000 | 2400 | 2600 |
Screen area /deck (m²) | 0,29 | 0,71 | 1,1 | 1,83 | 2,62 | 3,63 | 5,31 |
Space required (m²) | 0,4 | 1,2 | 1,6 | 2,5 | 3,6 | 5,2 | 6,8 |
Max. screen decks | 5 | 5 | 5 | 5 | 5 | 5 | 5 |
Connected load (kW) | 0,25 | 1,5 | 2,2 | 4 | 4 | 5,5 | 5,5 |
Screen cleaning systems | |||||||
Balls | 5 Decks | 5 Decks | 5 Decks | 5 Decks | 5 Decks | 5 Decks | 5 Decks |
Brushes | 5 Decks | 5 Decks | 5 Decks | 5 Decks | 5 Decks | 5 Decks | 5 Decks |
Air jet | 2 Decks | 2 Decks | 2 Decks | 2 Decks | 2 Decks | 2 Decks | 2 Decks |
Air jet + brushes | 2 Decks | 2 Decks | 2 Decks | 2 Decks | 2 Decks | 2 Decks | 2 Decks |
Ultrasound | 5 Decks | 5 Decks | 5 Decks | 5 Decks | 5 Decks | 5 Decks | 5 Decks |
Sieve attachment | 2 Decks | 2 Decks | 2 Decks | 1 Deck | 1 Deck | 1 Deck | 1 Deck |
Base plate (edge length) | 630 | 930 | 1100 | 1340 | 1340 | 1740 | 1940 |
Height (mm) | 850 | 1155 | 1480 | 1480 | 1500 | 1470 | 1580 |
1 deck weight (kg) | 140 | 490 | 700 | 980 | 1050 | 1690 | 1900 |
Height (mm) | 965 | 1280 | 1640 | 1640 | 1660 | 1590 | 1710 |
2 decks weight (kg) | 155 | 535 | 770 | 1060 | 1140 | 1780 | 2000 |
Height (mm) | 1080 | 1400 | 1800 | 1800 | 1820 | 1710 | 1840 |
3 decks weight(kg) | 170 | 580 | 840 | 1140 | 1230 | 1870 | 2100 |
Height (mm) | 1200 | 1525 | 1960 | 1960 | 1980 | 1830 | 1970 |
4 decks weight(kg) | 185 | 625 | 910 | 1220 | 1320 | 1960 | 2200 |
Height (mm) | 1310 | 1650 | 2120 | 2120 | 2140 | 1950 | 2100 |
5 decks weight(kg) | 200 | 670 | 980 | 1300 | 1410 | 2050 | 2300 |
POWER SPRINGS
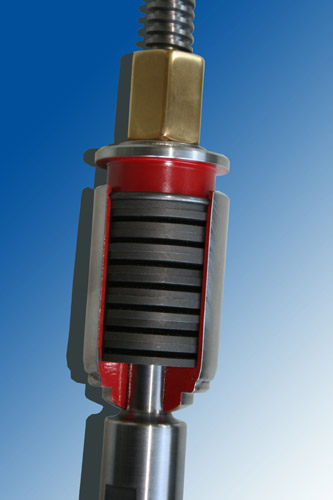
The dimensions of the gaskets can be negatively affected by the temperature of the materials, so that after a certain time the tensioning screws need to be manually tightened, especially on multi-deck machines. These springs automatically take care of the job.
The Power Springs consist of a case with set of springs fitted inside. The trapezoidal thread with a 4mm pitch, combined with a brass nut at the upper end guarantee outstanding mechanical durability and rapid fitting.
A colour code on the safety tensioning nut enables a simple sight test without turning the machine off. This makes it easy to check if the screw is providing sufficient tension.
A tumbler screening machine fully equipped with Power Springs and lifting device achieves the highest safety standards and the best material efficiency.
Original – Minox pneumatic lifting device for tumbler screening machines (trademark protected)
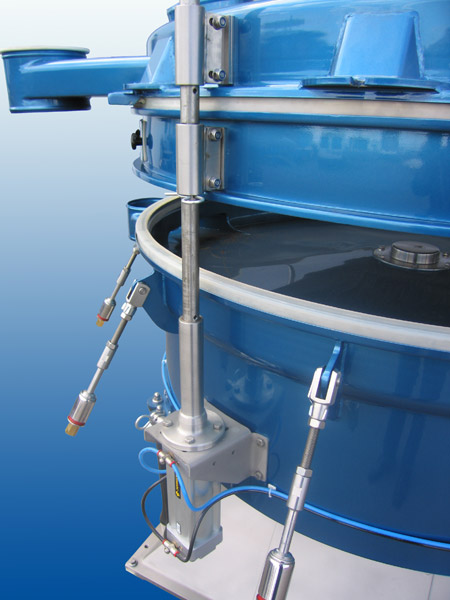
The MINOX machines in the MTS series are extremely robust and have long been equipped with genuine automatic screen centring.
The lateral flange this requires makes it easier to use a U-shaped gasket, which is simply passed over the screens. This means it is no longer necessary to go through the complicated process of gluing the flat gaskets used previously.
Nevertheless, until now a screen change could only be completed by manually removing the cover and the intermediate rings or by using a chain hoist or crane attached to the lifting rings on the screen casing. Despite the centred screen this makes changing the screen quite an arduous task, especially on large machines with 4-5 decks.
The latest invention from MINOX is a pneumatic lifting device enabling the intermediate rings and cover to be raised and lowered individually. Now the screen coverings can be exchanged quickly and easily or even just inspected.
Depending on the size of the machine and the number of screen decks, a 2 to 4 point lifting device is used. It is permanently attached to the tumbler screening machine and is ready to be connected to the air compressor, with pneumatic control for raising and lowering. As the lifting device is permanently attached it can be used at any time.
The pneumatic lifting device from MINOX can be retrofitted to almost all tumbler screening machines.
Effective screen cleaning guarantees uninterrupted operations
Particularly when screening fine particles the mesh can often become clogged by grains and dust or electrostatically charged. This can reduce performance and screening quality, sometimes considerably. In order to ensure uninterrupted operations the screen therefore needs to be cleaned in an appropriate way for the product. Due to their circular construction and three-way motion, tumbler screening machines are particularly suitable for rapid and easy fitting with the various screen cleaning systems.Air jet cleaning
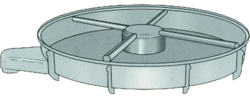
Air jet and brush cleaning
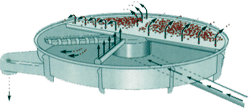
Brush cleaning
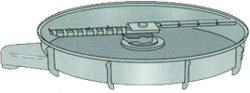
Bouncing ball cleaning
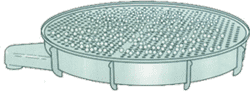
Sieve attachment
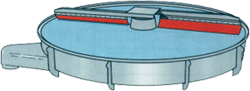